The embarrassing failure of Heathrow chiefs to protect the airport from power failure should be a stark warning for the future. But should those in charge of such an important facility have already learned from other airports’ experiences?
London Heathrow airport closed for 18 hours in March as a result of a power cut caused by a fire at a nearby electrical substation. Questions remain as to how such a power cut could force the entire airport to close for so long and why an international travel hub was vulnerable to a single point of failure while a data centre near Heathrow was able to operate as normal.
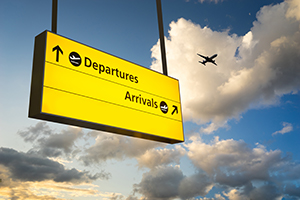
An investigation was launched by the government but many experts have suggested the crisis could have been handled better. Speaking on ‘Plugged In: the energy news podcast’, Simon Gallagher, the MD of UK Networks Services, questioned why the existing access to the power network couldn’t be more quickly reconfigured to provide power to the airport.
He also cited the example of Amsterdam’s Schiphol airport, which had problems in 2018 with high voltage fluctuations on their high voltage power supplies. They found they didn’t have enough generation to back up their terminals. The issues led them to put in more generation and introduce new testing procedures. They are now so serious about testing their supplies that they actually switch their terminals off from the main supply during the airport’s day-to-day operation to test their backup systems while thousands of passengers and staff go about their business unaware of what is going on.
“Why does Heathrow not have a lot of generation backup?” he asked Richard Sverrisson, the host of Plugged In. “So right next to Heathrow, in fact, within 20 meters of the fence of the substation where the fire happened, there’s a brand-new data centre… And that data centre will ultimately consume 150MW. So, three, four times what Heathrow consumes.
“And that’s connected via 66,000-volt cables to North Hyde, the exact same substation. But the big difference in that data centre and Heathrow is the data centre has got 100% generation backup. They’ve actually got twelve Rolls Royce [3MW back-up] generators … The generators fired up, they never lost operations. And they’ve got twelve generators, but they only actually need eleven. One of them is there to back up the backups.”
Plugged In podcast host and Editor-in-Chief of Montel News, Richard Sverrisson, said: “What happened at Heathrow in March is a wakeup call for the airport, the aviation industry and the UK authorities. It is unacceptable that one of the world’s busiest airports was knocked out for so long because of what appears to be a single point of failure.
“This episode of Plugged In provides much needed clarity about what we now know went wrong, what we still don’t know and a much clearer focus on which questions the UK authorities now need to answer.”
To listen to the pod please go to the Plugged In podcast homepage here.
All for the four day week
The testimonials from companies that say the four day week works keep rolling in. While the media has focussed on the bosses telling their employees that ‘work from home’ is being scrapped or reduced, in the electrical industry, that was never likely an option for most. But the four day week – would that work for you? In jobs that are productivity based rather than presence based – for instance manufacturing vs a hotel receptionist – it would seem possible to get the same, or even improved results, in a shorter time.
One pioneering company that has found this to be true is a small heating firm in the West Midlands.
Custom Heat made the groundbreaking decision to implement a four-day working week for its entire workforce while maintaining full pay, following a successful six-month trial. The move positions the company as the first in the heating and construction sector to adopt this progressive approach, setting a new precedent for the industry.
According to data from 4dayweek.co.uk, 56 out of 61 companies that tried the approach continued with it afterward.
These companies reported a 35% increase in revenue, 57% reduction in staff turnover, and 25% revenue growth over the previous year. Additionally, 83% found it easier to attract talent, while 66% reported reduced employee burnout.
Under the new arrangement, employees will receive 100% of their salary while working 80% of their contractual hours. Careful rostering ensures continued five-day service delivery with no impact on customer experience.
“We’ve been closely monitoring both employee wellbeing and business metrics throughout our trial period, and the results have been overwhelmingly positive,” said Lincoln Smith, Managing Director at Custom Heat.
“Our goal was to create a more sustainable work environment that benefits both our team members and our business outcomes.”
The company’s three-month review of the trial revealed significant benefits: staff retention improved dramatically with a 66.67% reduction in employee turnover compared to the same period in 2023; job applications increased by 250% when positions were advertised with the four-day week benefit; and despite employees working 20% less time, service and repair sales only decreased by 5%, while installation team sales were down just 1%.
Fuel costs decreased by up to 32% for some engineers, supporting the company’s sustainability goals, and staff absences due to sickness fell by 17.39% compared to the three months preceding the trial.
Engineers who participated in the trial reported significant benefits both professionally and personally.
Simon Scarfe, 56, who has been with Custom Heat for four years and in the gas industry for 25 years, initially approached the trial with caution. “I was skeptical and concerned about potential income loss,” said Mr Scarfe. “But once I understood the model, I was happy to try it. Having Wednesdays off allowed me to better balance work with my commitments as a community first responder and spend more time with family.”
You can find this article in the latest issue of Electrical Trade Magazine here.