Battery technology is driving the evolution of power tools. As manufacturers push for better performance and usability, the battery pack has become a key battleground. Designing a battery pack isn’t just about cramming in more energy, power tool OEMs need to strike a balance between durability, power and safety, while keeping up with technological advancements and industry trends.
Owen McNally, Principal Design Engineer at Alexander Battery Technologies, explores the key factors shaping next-generation battery packs for power tools.
Balancing Performance and Durability in Battery Design
The challenges faced by manufacturers in the power tool industry largely depend on the type of tool and its end-use application. As any tool manufacturer will understand, a drill used occasionally for DIY projects doesn’t have the same demands as a high-powered impact wrench on a construction site and the batteries inside them need to reflect that. Designing batteries for professional tools comes with higher expectations for sustained power, thermal management and resilience against real-world conditions.
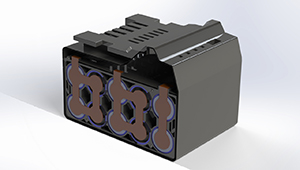
A key distinction in battery design for power tools is the difference in requirements between consumer-grade and professional-grade batteries. For consumer tools, cost-effectiveness and ease of use take priority. These tools are generally not subjected to heavy or prolonged use, so batteries don’t need to withstand constant high-power demands or extreme conditions. Instead, their design focuses on affordability, moderate durability and a straightforward user operation.
However, professional tools demand far more from their batteries. These tools are used on job sites where they can face harsh and unpredictable conditions. Their batteries need to deliver sustained high power without overheating while also withstanding drops, dust and moisture. Battery design engineers will incorporate essential features like ruggedised casings, high discharge rates and efficient thermal management to ensure long-term reliability and high-performance standards in tough environments.
Standardised battery platforms have helped OEMs simplify power tool ecosystems, offering broad compatibility and ease of use. However, these solutions don’t always meet the needs of professional and industrial applications, where performance and durability are key. As operational demands become more specialised, many manufacturers are looking beyond off-the-shelf options towards tailored battery solutions designed for real-world conditions.
For power tools used in extreme conditions, battery performance and durability are critical. A customised battery design can be the difference between reliability and failure. In one example, a manufacturer of high-torque tools used on oil rigs and in wind turbine maintenance was experiencing unacceptable failure rates due to harsh operating conditions, including frequent battery damage when the heavy tool was dropped.
By integrating a data logging feature within the battery management system, along with an accelerometer to detect drops, Alexander Battery Technologies developed a solution that disables the battery if it is dropped from a significant height. This added layer of protection helps prevent accidents and unnecessary returns, making the tools safer and more reliable for the end user.
One Size Doesn’t Fit All and The Shift Towards Custom Battery Solutions
As OEMs strive to differentiate their power tools, there’s a growing trend towards custom battery solutions. Standardised platforms like the Cordless Alliance System (CAS) are a practical choice for some companies providing an easy, cost-effective solution by offering a shared battery platform across multiple tools. However, this approach doesn’t allow for the flexibility and performance optimisation that many tools require, especially for use in industrial and heavy-duty applications.

Bespoke battery management systems enable OEMs to tailor power output, extend run times and add advanced functionality that standardised packs cannot provide. For instance, some tool batteries now feature Bluetooth connectivity, data logging and enhanced thermal protection, all designed to improve performance under demanding environments. These features are especially important for categories of power tools where battery operation is put to the test under intense usage conditions and directly impacts productivity and safety.
While a custom battery design gives the OEM full control and flexibility over the performance of their product, this route may present additional challenges, particularly around compliance and manufacturing costs. Regulations governing battery safety, transport and recyclability are becoming more complex and OEMs must ensure their products meet customer expectations as well as international regulatory requirements.
Despite these challenges, transitioning to a proprietary battery pack doesn’t need to be a costly or complex exercise. By partnering with a custom battery manufacturer, OEMs can develop high-performance, cost-effective solutions that comply with industry regulations while being precisely optimised for market viability and long-term reliability.
Selecting the Right Battery Technology for Power Tools
When designing battery-powered tools, OEMs must carefully evaluate the advantages and trade-offs of different cell formats when specifying the battery pack. Cylindrical cells remain the industry standard due to their robustness, high discharge rates, and mechanical durability, making them a reliable choice for both consumer and professional-grade tools. They are also easy to manufacture at scale, providing consistent performance and cost-efficiency for power tools that require high power output and resilience to impact and vibration.
For applications where compactness, weight reduction, and heat dissipation are critical, some manufacturers are exploring pouch cells. These can offer higher energy density in a smaller footprint and, in some cases, support faster charging times. However, pouch cells lack structural rigidity, making them more susceptible to damage and requiring additional packaging to ensure durability in real-world use. This adds complexity to battery pack design, particularly for tools that experience high-impact use or extreme conditions. For this reason, cylindrical cells remain the preferred choice for battery design engineers seeking long-term reliability and user safety in power tools.
Navigating Regulatory Compliance and Shipping Restrictions
One of the most significant concerns for OEMS when exploring the option for a custom battery design is meeting global shipping and safety regulations. Power tool manufacturers must carefully navigate these regulatory frameworks, especially when selling internationally. Batteries exceeding 100 watt-hours are classified as dangerous goods, requiring special packaging, labelling and certifications. In addition, some regions impose certifications, such as UL or CE, making compliance an important consideration in product development and distribution.
As battery capacities increase, it’s also important to consider the environmental impact and recyclability of batteries. There’s increasing pressure on manufacturers to develop batteries that can be recycled more efficiently and are less reliant on finite materials like lithium and cobalt. With growing pressure on the industry to meet sustainability goals, power tool manufacturers must design battery packs with recyclability in mind and explore second-life strategies to reduce environmental impact.
Ensuring compliance without compromising performance or cost efficiency requires a deep understanding of both technical and regulatory landscapes. Custom battery pack manufacturers with expertise in international standards and shipping regulations can help OEMs streamline certification, avoiding costly delays and develop and ensuring a market-ready battery solution. An experienced battery partner builds compliance into the design process early, helping OEMs avoid costly redesigns, certification delays and supply chain disruptions.
Innovations Shaping the Future of Power Tool Batteries
While cylindrical cells continue to dominate, emerging battery technologies could bring significant advancements in performance, safety, and efficiency for power tools. One of the most promising developments is AI-powered battery management systems (BMS), which enable batteries to monitor their own health, optimise power delivery based on usage patterns, and regulate temperature in real time. This technology enhances both battery lifespan and tool performance, ensuring more consistent power output even in demanding environments.
Another innovation gaining traction is the tabless cell design, which aims to reduce internal resistance and heat generation. Unlike traditional cylindrical cells, where tabs limit current flow, this design allows for faster charging and discharging, improved efficiency, and better thermal management. While still in its early stages, the technology has the potential to improve power tool performance and battery longevity if manufacturers can scale production cost-effectively.
Silicon anode batteries are also drawing attention, offering higher energy density, longer runtimes, and faster charging. Historically, these batteries have faced challenges with swelling, sometimes expanding up to three times their original size. However, recent design improvements claim to have mitigated this issue, making them a potential game-changer for power tools if they prove stable in real-world applications.
Looking further ahead, solid-state batteries could introduce even greater safety and efficiency by replacing traditional liquid electrolytes with a solid material. This change could reduce the risk of thermal runaway while also increasing energy density and cycle life. However, solid-state technology remains expensive and is not yet widely scalable for power tools. If manufacturers can overcome these hurdles, it could become one of the most significant advancements in battery technology in the coming years.
The Advantage of a Knowledgeable Battery Partner
Innovation is key to staying competitive in the power tool market, and battery technology is evolving fast. Advances in AI-powered BMS, high-energy-density chemistries, and new cell designs bring opportunities to improve performance, safety, and user experience. But integrating these advancements into a reliable, manufacturable solution isn’t always straightforward. Standardised, off-the-shelf battery options can only go so far, and for many OEMs, they no longer provide the performance, durability, or flexibility needed for demanding applications.
A strong battery partner helps OEMs make the right choices at every stage, from defining mechanical and electrical specifications to ensuring regulatory compliance and managing logistical considerations. The right expertise ensures that battery packs are safe, durable, and optimised for real-world conditions, while also helping to avoid costly delays or design limitations that could impact product success.
Beyond technical expertise, an experienced partner offers valuable insight into emerging technologies and market trends, helping OEMs future-proof their designs and stay ahead of shifting regulations. With battery technology playing an ever-greater role in product differentiation, working with a specialist ensures power tool manufacturers can deliver high-performance, regulation-ready products with confidence.