The benefits of working in an alliance
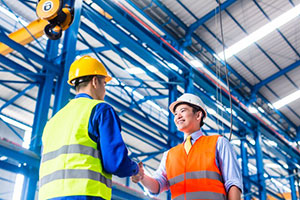
A chance encounter between Ford CEO Alan Mulally and Toyota president Akio Toyoda sparked conversations that led to the collaborative production of a hybrid system for trucks. As unlikely and improbable the partnership between these two competitors appeared at first glance, alliances between businesses often prove to be beneficial to both participants and the end client. Here, Brian Donaldson, business development authority at engineering solutions provider, Boulting, explains the benefits of working with an alliance of companies. Although there are many definitions for the word alliance, the one consistent message is the necessity of trust. In my opinion, an alliance doesn’t necessarily constitute a legal contract or a joint venture, it is simply an understanding that those involved will be working for the whole, rather than for individual gain. This is the defining factor that sets an alliance apart from a supplier-customer relationship. Integrated project delivery (IPD), is one way in which to manage an alliance. The practice promotes collaboration which is essential to a successful project, as each member of the overall team should share goals and be working to achieve the best possible end result. Working for the whole Working as part of an alliance can deliver a better end result, as it encourages businesses to bring in experts to the job that can deliver elements of the project that may lie outside of their core competencies, while sharing knowledge with one another. For this reason, contractors may find that an alliance opens doors into new sectors. For clients, many find it simpler and easier to have a single point of contact (SPOC) to communicate with, rather than trying to piece all the information together from several channels who may not be effectively communicating. In this way, a managed alliance can deliver a smoother service throughout the project life cycle. These results are delivered through trust, clear goals set at the start of the project and a structured way of working that means each contractor or supplier is focused on delivering the best end result possible, on time and under budget. Integrated project delivery (IPD) is one way of ensuring collaboration is achieved. IPD aligns each collaborators interests, objectives and practices to ensure every individual, team or business will become equally invested, sharing risk and profit in a fair and transparent manner. This could involve using target costs and including the client as a member of the team. Trust Because trust and good communication is vital to delivering effective collaboration, the largest challenge is obtaining this trust with a new business, perhaps without having any part in who is appointed. Communication tools and methods including getting every involved individual working in the same room, or extremely visual project management such as a physical whiteboard, can provide a crucial base to work from. Just because management knowthe overall project timeline, don’t assume that it’s the same for each team member. Inefficient communication can produce sub-par end results or even for the project to overrun or go over budget due to issues not being properly encountered for. If the trust fails, so do collaborative behaviours — and this puts the project at risk. Throughout its years of experience, Boulting has not only built up a long list of companies in all sectors with which it enjoys an excellent relationship, it also knows the most effective ways of working in an alliance such as insisting on regular face to face meetings, using project management tools and ensuring safety remains at the forefront of all projects. This aids it in producing successful project outcomes that meet client key performance indicators (KPIs). A good alliance, where each party is equally invested in producing the best possible outcome, can be achieved through working with companies that have been recommended, or have been referred by a trusted middle man. This can result in a smoother project delivery, alongside a superior end result. Regardless, some of the most successful collaborations in history, such as that of Ford and Toyota, can come as a surprise even to themselves. For more information about Boulting’s work in alliances, or to find out more about how your engineering project could benefit from the expertise that an alliance can provide, visit www.boulting.co.uk.
Designing for hazardous environments
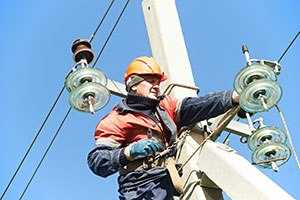
When Mount Vesuvius erupted in AD79, the citizens of Pompeii were not prepared for the devastation that followed. Having lain dormant for the last 71 years, the Italian authorities continue to prepare for the next eruption from one of the most dangerous active volcanos in the world. Here, Paul Mannion, project engineer at engineering solutions provider Boulting, explains the considerations that should be made when designing for builds in hazardous environments. The Dangerous Substances and Explosive Atmosphere Regulations 2002 (DSEAR), defines a hazardous area as “any place in which an explosive atmosphere may occur in quantities such as to require special precautions to protect the safety of workers”. It is vital that precautions are taken when constructing, installing and using apparatus in areas that have been defined as hazardous. In the UK, the regulation BS EN 60079 part 10-1 and part 10-2 are used to determine the area classification, a method of analysing the environment where explosive gas and or dust atmospheres may occur. The DSEAR scope is extended with BS EN 60079 part 14 detailing the design, selection and erection of electrical installations within a hazardous area and BS EN ISO 80079-36 to incorporate non-electrical sources of ignition and mobile equipment that could also pose an ignition risk. Identifying hazardous environments Hazardous areas are classified under six zones. Three zones associated with gas are classified under Zone 0 and are areas where an explosive gas atmosphere is present continuously or for long periods of time. Zone 1 is an area where an explosive gas atmosphere is likely to occur in normal operation, while Zone 2 covers areas where an explosive gas atmosphere is not likely to occur in normal operation and if it occurs, will only exist for a short time. The other three zones are associated with dusts, which are either flying and explosive, conductive or non-conductive. It’s worth noting that 80 per cent of dusts are combustible. The associated three zones are Zone 20, an area where ignitable concentrations of combustible dust or ignitable fibers/flyings are present continuously or for long periods of time under normal operating conditions; Zone 21 an area where ignitable concentrations of combustible dust or ignitable fibers/flyings are likely to exist under normal operating conditions and; Zone 22, an area where ignitable concentrations of combustible dust or ignitable fibers/flyings are not likely to exist under normal operating conditions. Areas that do not fall under the six outlined categories are classified as non-hazardous or ‘safe areas’. Any facility that processes, uses or manufacture’s materials that may give rise to a flammable atmosphere, such as gas, mist, liquid and small fibres (dusts), may have a potentially explosive atmosphere and therefore fall into one of these six zones. Industries that may have an explosive atmosphere, include food manufacturing, power generation, water treatment, oil and gas, chemical manufacturing and pharmaceutical. Boulting’s qualified electrical engineers always visit a site before beginning work on a project to ensure the relevant protection systems are in place. By visiting the site beforehand and conducting the appropriate risk assessments, Boulting’s engineers can ensure that the build is specifically designed for that unique environment, taking into consideration any potential risks. As part of their role, Boulting ensures its engineers are aware of the latest legislation and safety requirements associated with the particular hazardous environment. While areas classified as Zone 0 or Zone 20 continuously face the potential for the creation of an explosive gas or dust atmosphere, work still needs to be conducted in these areas. To continue this work safely, the equipment used needs to be weighted so that there is no chance of creating explosions. Equipment should be designed in such a way that it is stringently safe and includes current limiting devices to stop sparks. The equipment that will be used should be chosen and tested as early in the design process as possible. Before equipment can be used in any hazardous area, it must undergo a programme of rigorous checks and testing by a registered ATEX test house. ATEX is the name given to two European directives that aid in controlling explosive atmospheres. The first, Directive 99/92/EC (ATEX 137) assess the minimum requirements for improving health and safety protection for workers in potentially explosive environments. Directive 94/9/EC (ATEX 95) looks at the laws concerning equipment and protective systems intended for use in potentially explosive environments. Constructability When constructing a new facility or working in an existing environment, it is important that the installation of new components is done using the most efficient techniques to reduce the risk of incidents. Modularisation is a technique often used by Boulting. This method sees equipment or parts of a facility built offsite and installed at a later date, taking the risk out of working on a hazardous site. In addition to constructing in a safer environment, modular builds reduce site disturbance, minimise waste, are more cost effective and allow for far greater design flexibility. Construction of the overall build can also take place much quicker as modular builds occur simultaneously to the main build. Boulting is a leading provider of mechanical and electrical prefabrication and modularisation services, which it completes at onsite workshops and fabrication sites such as its 9000m2facility in St. Helens. Techniques used include pre-assembled units, skids and building services modules. These processes allow us to standardise installation, helping to maintain high quality standards. Maintainability While ATEX testing is vital to identify and resolve potential risks at the start of a project, it is important that inspections continue to take place on a regular basis throughout the equipment’s lifespan. With the development of new software these inspections have started to incorporate risk based elements which are identified by HSE. This method of inspection looks at the type of protection used, the installation factors i.e. vibration, corrosive, outdoors etc in addition to common manufacturer/model failures Engineers should factor in the production of a schedule for periodic inspections at the design stage. At Boulting, we provide clients with a digital cloud based system where
Refurbishing electrical systems – Boulting’s infographic sheds light on electrical refurbs
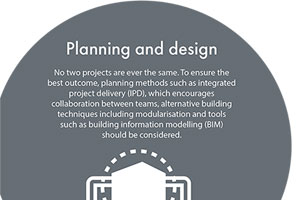
Award winning engineering solutions provider, Boulting, has released an infographic detailing ten top tips for engineers who are carrying out electrical refurbishments. The infographic highlights the most important aspects of the refurbishment process and educates plant managers about the importance of each stage. The infographic is free to download from the Boulting website. Every piece of electrical equipment within a plant will require regular maintenance and refurbishment. As a result, there is no one size fits all process for refurbishment as all plants and the equipment inside them are different. The areas for consideration, however remain the same. Boulting understands that, regardless of a project’s scale, a tried and tested refurbishment protocol is essential toensure successful completion of a project and that the site remains safe at all times. Its new infographic allows engineers to share in its wealth of knowledge and experience, by providing ten key areas to consider before beginning an electrical refurbishment. Topics in the infographic include, surveys, impactof downtime and the importance of having a contingency plan. “Electrical refurbishments are an integral part of our business and we are proud of our reputation of executing these complicated jobs to an extremely high standard” explained Paul Meagh, electrical and instrumentation director at Boulting. “The maintenance of electrical equipment is often easily overlooked, but it is essential for the equipment to be running as efficiently as possible, both to ensure running costs are minimised, but also to extend the life of existing assets. “Asset life extension is a popular concept for plant engineers, who wish to have long intervals between replacingequipment. As their current equipment has already been purchased, commissioned and is often working without fault, our aim is to keep the equipment in use for as long as realistically possible. Regular maintenance and effective refurbishment is a crucial aspect of this.” continued Meagh. For more information on Boulting’s services and products, visit www.boulting.co.uk.
Boulting appoints new HR director
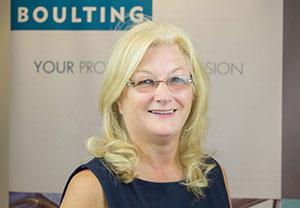
Warrington-based engineering solutions provider, Boulting Ltd has promoted human resources (HR) manager, Michelle Stott, to the position of HR director. Stott, who has over 20 years HR experience and has previously worked for Marks and Spencer and the Environment Agency will take up the role to reinforce the organisation’s commitment to its staff across the UK. Stott, who graduated from Liverpool John Moores University with a degree in Human Resource Management and Psychology, began her HR career at Royal and SunAlliance and has worked both in the UK and Overseas for north-west based organisations her entire career. Moving to Boulting Ltd in 2013 as HR and resourcing manager, she has supported the organisation with employee relations and ongoing recruitment requirements. Stott is Charted Institute of Personnel and Development (CIPD) qualified and also holds numerous employee management accreditations including, Myers & Briggs Type Indicator (MBTI) and 16 personality factors (16pf). Throughout her career, Stott has designed and developed assessment tools for line managers and outplacement workshops as well as implementing an online tool for recruitment strategy. “In the five years that I have worked for Boulting, I have always been impressed with the future prospects of not only the company, but the organisation’s employee skills set too,” Michelle Stott said. “As HR director I will look to reaffirm the company’s people management processes as well as solidify new schemes, such as a formal mentorship programme and increased school liaison work. “Government studies report that the engineering sector is facing a skills crisis like never before,” continued Stott. “The industry needs around 186,000 skilled recruits each year, until 2024, to help bridge the gap. At Boulting we understand the need to develop our current staff as well as consider new ways to tackle the skills gap and improve diversity across the engineering sector as a whole. “Our dedication to our employees continuous professional development (CPD) and our ongoing apprenticeship scheme is just the starting point of our investment in engineering careers and the evolving industry in which we work,” Stott added. “Boulting Ltd is committed to its employees,” Josh Groake, deputy managing director at Boulting commented. “By promoting Michelle into the role of HR director, she will lead a dedicated human resources team that will work to support and guide our staff across the UK and beyond. Michelle will provide a wealth of knowledge and experience to our directorial board and some of the ideas and plans she has moving forward will continue to set Boulting apart as a dedicated and valuable employer.” Boulting Ltd is a multi-disciplined engineering solutions provider, operating across a diverse range of industry sectors in the UK and abroad. The organisation employs over 950 staff throughout the UK at its regional sites. To find out more information about Boulting visit www.boulting.co.uk.